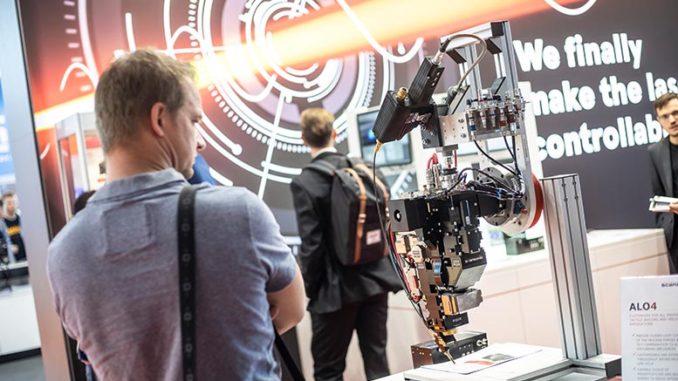
Laser marker processes are routinely used for industrial purposes nowadays. Time and again, however, there are new technical, environmental and economic challenges. „These come from marking small and sensitive workpieces,“ reports Dietrich Tönnies, Product Line Manager for laser markers at Coherent. „But also from achieving good marking results with new materials and on uneven moulded parts.“ As an expert in the field, he observes that the quantity of information to be marked onto items is constantly increasing, therefore the speed of laser marker facilities must also be further increased, he believes. „Laser marker facilities should be low-maintenance and reliable,“ adds Lars Meier, Product Manager in the laser division at Bluhm Systeme. According to him, they must also be extremely safe, in terms of both operation and production. Many LASYS 2020 exhibitors will be offering solutions to these challenges from 16 – 18 June 2020 in the Stuttgart trade fair halls. As an international trade fair concentrating on laser material processing, LASYS is the right place for all those who are looking for economical production solutions using light as a „tool“, or who want to find new and improved production methods for material processing.
Laser marker systems – great for customising products
When it comes to laser marking systems, „laser technology can be used in an increasingly customised way and for many different materials, areas of application and sectors,“ emphasises Mirko Waldschmidt, sales manager for marking systems at Gravotech. For the diverse target user groups at LASYS, marking components with lasers has now become indispensable. These target groups include the automotive sector, mechanical engineering, the electrical and electronics industry, the optical industry, plant and apparatus construction, the metalworking and metal processing industry, medical technology, the plastics industry, toolmaking and mouldmaking and the semiconductor industry.
Component traceability and product customisation are boosting the laser marking systems market. With the growing trend of personalisation, many mass products (such as smartphones or their protective cases) can be customised, i.e. given their own name or label. Whether products are made of plastics, metal, glass, ceramics or organic materials, such as leather or wood, now makes almost no difference, as laser markers are versatile and can be used across a wide range of materials.
Head for the future in an environmentally friendly way with natural branding
What is known as natural branding is currently sparking great interest. It involves laser marking food such as fruit and vegetables, as well as bread rolls, cheese, eggs, etc., in an environmentally friendly manner – without labels. With eSolarMark plus, Bluhm Systeme has developed a laser system for this purpose that marks four fruits simultaneously in the blink of an eye. Even if, for instance, you have apples of different sizes, this can be compensated using a 3D focus of up to 40 mm, so that the marking is always of the same quality. Bluhm Systeme also already has experience with laser printing on edible straws, in the spirit of using less plastic to reduce the strain on the environment. Speed is required here, as up to 50,000 straws an hour leave the dual-nozzle extruder.
Time taken by laser marking reduced by 50 per cent
Coherent’s PowerLine E Twin is also concerned with speed. The laser specialist has developed a new solution in which two laser marking units mark a workpiece together. According to Dietrich Tönnies, „what is special about this is that the system is controlled via hardware and software interfaces, as with a single laser marker. Both integration and operation are very easy. The system requires only a marker formula and a layout, and automatically shares the work between the two marking units. This can reduce the time taken by marking by up to 50 per cent, without increasing the complexity of the overall system. This leads to a considerable reduction in the overall operating costs of the unit.“ Coherent covers a wide range of laser marking applications with its PowerLine series. Agriculture alone is a lucrative target market. Only recently, the company announced a new partnership collaboration, which involves optimising a new plastic for animal ear tags in terms of impact on health and ease of laser marking. Tönnies gives another example application from the electronics industry, saying that „the market for high-power LEDs, the production of which must be fully traceable, is constantly growing. The interior lighting of modern cars now relies exclusively on LEDs (light-emitting diodes). In LED production, our laser markers inscribe leadframes (supports) with tiny 2D matrix codes, which are made up of points of just 43 micrometres in diameter.“
Easy integration onto production lines
In the field of production automation, marking parts efficiently invariably plays a key role when it comes to traceability. Gravotech has developed a compact and safe solution for this – the Mini-Inline laser shield. Mirko Waldschmidt explains that „it makes using laser technology on production lines easier and considerably more efficient than before. The Mini-Inline is mounted on the laser head and forms a kind of protective barrier between the laser head and the workpiece to be marked. The systems no longer have to be housed due to the open laser radiation. They can be designed more compactly and are easily accessible for maintenance work. What is more, smoke from the laser can be directly absorbed by the funnel and does not get into the system. This results in a massive improvement in system safety and employee protection.“
Flexible registration plates for electric cars
The transformation in car production from the combustion engine to the electric motor has brought with it new requirements for laser marker facilities. For example, electric car manufacturer e.GO Mobile AG was concerned with the integration of a laser marking system. To mark the electric vehicles, the automotive manufacturer uses Bluhm Systeme’s LFM 100 laser foil marker. „It is an innovative combination of label printer and laser system that marks flexible type plates using a laser. The saltwater-proof and adhesive lacquer foil is cheaper and more flexible than the standard stainless steel type plates,“ emphasises product manager Lars Meier. „A requirement of this project was integrating the device into the system of the user. The print information now comes directly from the user’s system,“ continues Meier. According to Meier, machine networking is becoming increasingly important, particularly for the future. Here, using software to integrate laser marking systems into the customer’s system is continuing to become a focus.
USP laser offers the ideal solution for medical technology
The start-up LightPulse Laser Precision relies on marking using an ultra-short pulse (USP) laser. It will be a co-exhibitor at the Photonics BW joint initiative stand at LASYS 2020. Particularly strict requirements are stipulated for product identification (UDI: Unique Device Identification) in the medical technology sector. Traceability, long-term stability and corrosion-resistance are crucial factors that must be taken into consideration when marking medical instruments and implants. Dr.-Ing. Christian Freitag, CEO of LightPulse, explains that „black marking is highly suitable here because it is very high-contrast and corrosion-resistant, and remains legible for a long time. In addition, it has a high viewing angle stability. USP lasers create a rough texture on the marked surface in the micrometre and nanometre range, which decreases the reflection of the ambient light. This results in a stable black colour.“
Expert knowledge in demand
There are barely any materials left that coherent laser light is unable to mark.
„Marking fibre composites is still a challenge, due to the non-homogeneous structure of the material.“ Dr Freitag has found out that „the strategies with which materials can be marked differ particularly regarding the thickness of material that can be removed when marking with laser light. To get the optimum marking result,“ the expert further explains, „the laser parameters must be set correctly, depending on the material properties of the composites. This requires dedicated expert knowledge.“ The founder of the company obtained this knowledge at the Institut für Strahlwerkzeuge (IFSW) of the University of Stuttgart, which, in 2020, will be organising the Stuttgart Laser Technology Forum for the 11th time. This is a highlight of the LASYS accompanying programme and, just like the trade fair, is intended for an international audience.
Bild & Text: messe-stuttgart.de